Warehouse system workflow
1. Confirm the order After the customer confirms the order The data will be sent to the AGV system.
2. Planning to choose When the system receives the order The staff will make a product distribution plan in the intelligent AGV system based on time, express order, online store, platform, same product, same order. the same product There are different orders (more than 2 pieces).
3. Wait to receive After the plan has been prepared. Employees just wait for the robot to arrive on the desk. Then select the products and quantities on the shelf specified by the AGV system, then place them in the picking cart specified by the AGV system to complete the picking.
4. Arrange the goods. The picking basket will flow to the packing place. And the packing staff will scan the code of the basket first and do the second check according to the display of the AGV system, check and confirm it is correct. Then scan the product barcode to print a cover sheet for that order.
5. Complete packaging After the inspection is complete Packers will select boxes or bags for packaging according to the product form. and attach the order cover
Highlights of the AGV warehouse system
good performance
Step-by-step implementation of picking, printing and packaging systems It can greatly reduce errors and improve work efficiency. Reduce 50 of the same order from the packing staff and carry out the sorting of one item in order. if there is an error Rearrange one or fewer items. must check again Either during the sorting or reordering process Verification process after error will affect the progress of the entire package group. that make the problem bigger This type of problem is a difficult problem to solve. And it's also an endless loop problem.
save human resources
saves manual picking And avoid the situation where the same picker has to pick multiple times. If there are 50 orders, the picker must search for the item once. If there are 4,000 orders/day, each best-selling item needs to search 80 times, which is wasteful. human resources The storage system can use the same order and the same type of goods only once. The products can be taken out and packed together or arranged in the warehouse.
save time
It saves time for the store manager team to log in to the back of the house to receive and sort orders. and to avoid mistakes Only 50 order cover sheets will be printed at a time.
correct inventory
The AGV system will automatically update the stock count at all times. This effectively improves inventory accuracy. It also alerts employees in time for items that are out of stock and need to be replenished. This solves the problem of losing leads in the store. due to lack of physical inventory caused by manual action
financial
It saves the time that financial personnel need to manually retrieve orders. and avoid wasting time manually reducing inventory for a single product. loss of manpower Refunds caused by out-of-stock inventory and other bad reviews and after-sales errors achieve accurate and timely reporting of financial status in monthly reports.
easy to follow
Able to keep track of the current order status at all times And can check the turnover of the store and the sales of various products. Get on time for slow moving goods. Employees are alerted to avoid inventory hoarding and facilitate work management at any time. Using the automatic inventory allocation function To avoid unnecessary problems caused by manual inventory allocation. and frequent errors caused by not updating physical inventory.
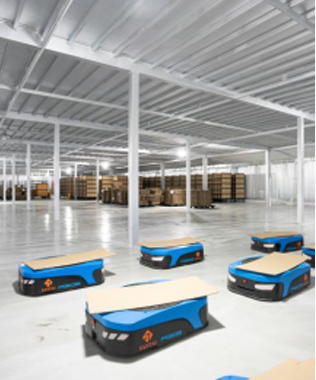
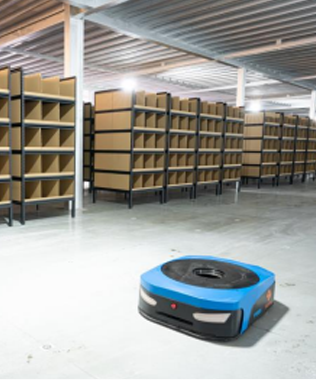
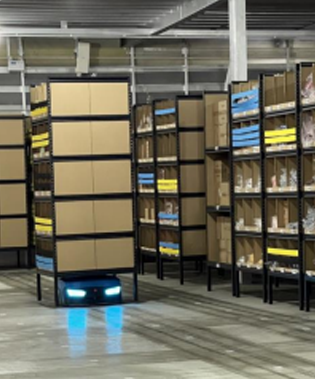
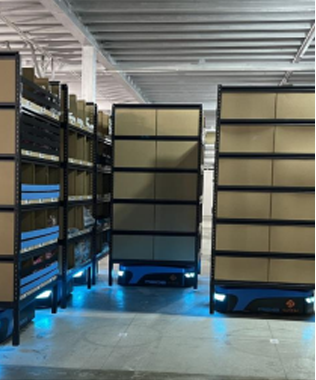
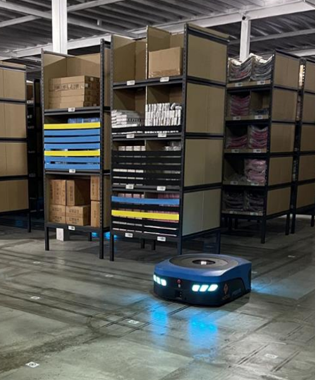
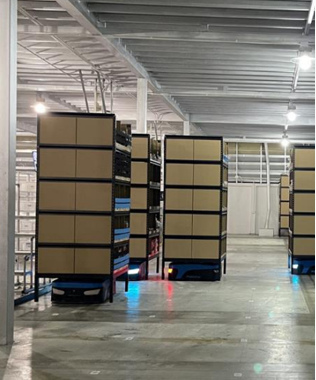
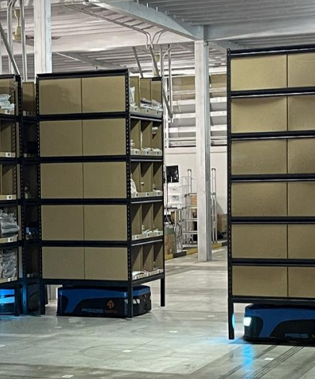
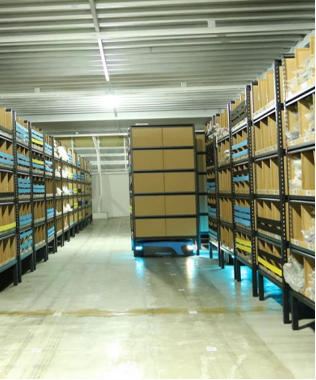
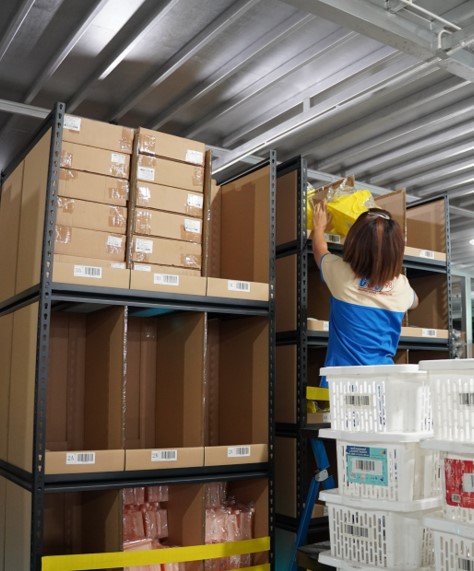
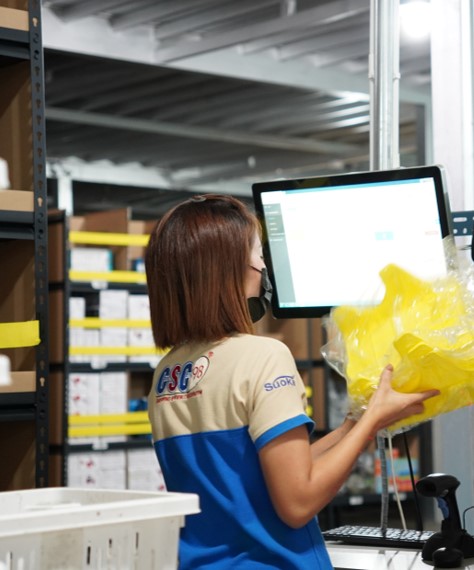
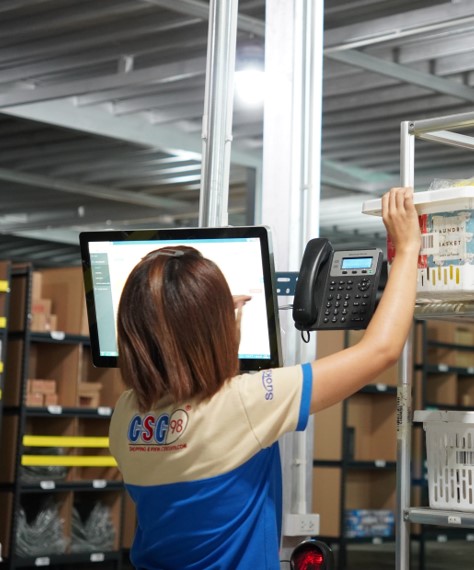
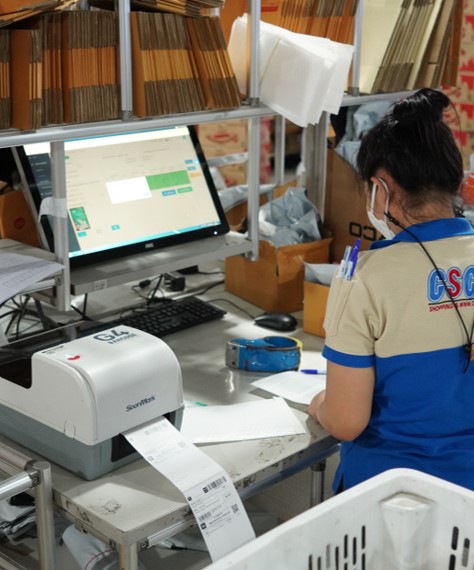